Integrating Total Productive Maintenance and Industry 4.0 for Optimal Performance
Discover how integrating Total Productive Maintenance (TPM) with Industry 4.0 can enhance your manufacturing operations and achieve optimal performance. Learn about the benefits of TPM consulting and how it can help your organization thrive in the digital age.
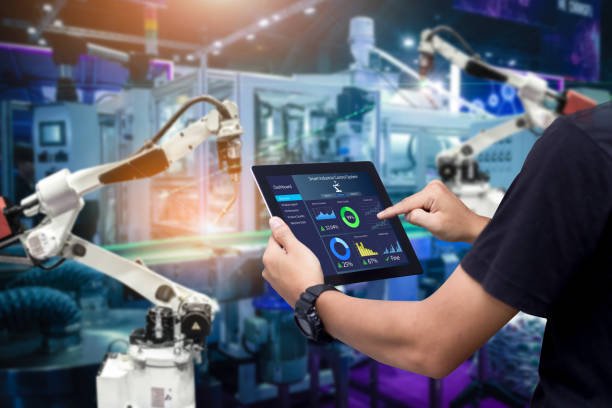
In today's rapidly evolving manufacturing landscape, staying competitive requires not only embracing cutting-edge technologies but also implementing efficient maintenance strategies. Total Productive Maintenance (TPM) is a holistic approach that aims to optimize equipment effectiveness, minimize downtime, and improve overall operational efficiency. When combined with Industry 4.0 principles, TPM can unlock a new level of productivity and performance for organizations. In this article, we will explore the integration of TPM and Industry 4.0, the benefits it offers, and how TPM consulting can support your journey towards optimal performance.
Understanding Total Productive Maintenance (TPM)
Total Productive Maintenance is a comprehensive maintenance strategy that originated in Japan and has gained popularity worldwide. It emphasizes the involvement of all employees, from operators to management, in maintaining and improving equipment and processes. The primary objective of TPM is to eliminate equipment failures, reduce downtime, and enhance productivity.
The Pillars of Total Productive Maintenance
TPM is built on a foundation of eight essential pillars, which serve as guiding principles for organizations:
- Autonomous Maintenance: Empowering operators to perform routine maintenance tasks, inspections, and minor repairs on their equipment.
- Planned Maintenance: Implementing preventive maintenance activities based on data and regular scheduling to minimize unscheduled downtime.
- Focused Improvement: Encouraging employees to identify and address issues that hinder productivity through small-scale improvement initiatives.
- Early Equipment Management: Incorporating maintenance considerations during the design and acquisition of equipment, ensuring long-term reliability and ease of maintenance.
- Quality Maintenance: Enhancing product quality and reducing defects by preventing equipment malfunctions and abnormalities.
- Education and Training: Providing comprehensive training programs to equip employees with the necessary skills and knowledge to perform maintenance tasks effectively.
- Safety, Health, and Environment: Ensuring a safe and healthy work environment while adhering to environmental regulations.
- Administrative and Office TPM: Extending the principles of TPM to administrative and office functions, optimizing processes and reducing waste beyond the shop floor.
By implementing these pillars, organizations can create a culture of continuous improvement, maximize equipment effectiveness, and achieve operational excellence.
Industry 4.0: The Fourth Industrial Revolution
Industry 4.0, often referred to as the fourth industrial revolution, represents the integration of digital technologies into manufacturing processes. It encompasses concepts such as the Internet of Things (IoT), Artificial Intelligence (AI), big data analytics, cloud computing, and automation. Industry 4.0 aims to create "smart factories" where interconnected systems and machines can communicate, analyze data in real-time, and make autonomous decisions.
Synergies between TPM and Industry 4.0
Integrating TPM with Industry 4.0 can create synergistic effects that revolutionize manufacturing operations. By leveraging the power of real-time data, advanced analytics, and automation, TPM can be enhanced in several ways:
- Predictive Maintenance: Industry 4.0 technologies enable the collection and analysis of vast amounts of data from equipment sensors. This data can be used to predict equipment failures and proactively schedule maintenance, minimizing unplanned downtime.
- Condition Monitoring: IoT-enabled sensors can continuously monitor equipment conditions, providing real-time insights into performance, temperature, vibrations, and other key parameters. This allows early detection of abnormalities, enabling timely intervention before major issues occur.
- Remote Monitoring and Control: With Industry 4.0, equipment can be remotely monitored and controlled, reducing the need for manual inspections and interventions. This not only saves time but also improves safety by minimizing exposure to hazardous environments.
- Digital Work Instructions: Industry 4.0 technologies enable the creation and deployment of digital work instructions, providing operators with intuitive, step-by-step guidance for maintenance tasks. This improves accuracy, reduces errors, and facilitates knowledge transfer.
- Data-Driven Decision Making: By integrating TPM with advanced analytics and AI, organizations can gain actionable insights from the vast amounts of data generated by their equipment. This enables data-driven decision making, optimizing maintenance strategies and improving overall equipment effectiveness.
The Benefits of Integrating TPM and Industry 4.0
The integration of TPM and Industry 4.0 brings numerous benefits to organizations seeking optimal performance and competitiveness in the digital age. Some key advantages include:
- Improved Equipment Reliability: Predictive maintenance and condition monitoring techniques reduce the risk of unexpected breakdowns, prolonging the lifespan of equipment and ensuring its optimal performance.
- Reduced Downtime: Proactive maintenance scheduling and early detection of abnormalities minimize unplanned downtime, maximizing production output and overall equipment effectiveness.
- Enhanced Operational Efficiency: The combination of digital work instructions, remote monitoring, and data-driven decision making streamlines maintenance processes, reducing errors, and improving productivity.
- Lower Maintenance Costs: By optimizing maintenance activities and reducing the frequency of unplanned repairs, organizations can achieve significant cost savings in terms of spare parts, labor, and equipment downtime.
- Empowered Workforce: TPM fosters a culture of employee involvement, encouraging operators to take ownership of equipment maintenance. The integration with Industry 4.0 technologies provides them with advanced tools and insights, enhancing their capabilities and job satisfaction.
The Role of TPM Consulting in the Integration Process
Successfully integrating TPM with Industry 4.0 requires expertise and a strategic approach. TPM consulting services can play a vital role in supporting organizations throughout their transformation journey. Experienced TPM consultants bring deep knowledge of maintenance best practices, change management techniques, and the latest technological advancements.
Key Areas of TPM Consulting Support
- Assessment and Gap Analysis: TPM consultants conduct comprehensive assessments of an organization's current maintenance practices and identify areas for improvement. They help organizations understand the readiness for Industry 4.0 integration and develop a roadmap for change.
- Strategy Development: TPM consultants work closely with organizations to develop tailored strategies that align TPM principles with Industry 4.0 technologies. This includes defining key performance indicators, setting targets, and establishing implementation plans.
- Training and Education: TPM consulting services provide training programs to equip employees with the necessary knowledge and skills to embrace new technologies and effectively contribute to TPM initiatives.
- Technology Selection and Implementation: TPM consultants assist organizations in selecting and implementing the right Industry 4.0 technologies that align with their specific needs and objectives. They ensure seamless integration with existing systems and processes.
- Change Management: The integration of TPM and Industry 4.0 often requires a cultural shift within organizations. TPM consultants help manage this change by facilitating communication, providing guidance, and fostering employee buy-in.
By leveraging the expertise of TPM consultants, organizations can navigate the integration process smoothly and unlock the full potential of TPM and Industry 4.0 synergy.
Conclusion
In the era of Industry 4.0, manufacturers must continuously strive for operational excellence and leverage technological advancements to stay competitive. The integration of Total Productive Maintenance and Industry 4.0 offers a powerful combination that drives optimal performance, equipment reliability, and cost savings. By embracing the principles of TPM, leveraging Industry 4.0 technologies, and seeking support from TPM consulting services, organizations can embark on a transformative journey that propels them towards sustainable success in the digital age.
What's Your Reaction?
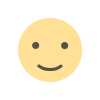
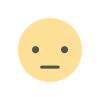
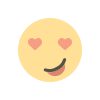

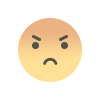

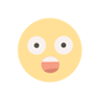